Niobium in martensitic steel
- In martensitic steel strength is directly related to the carbon content. Strength contributions of grain refinement and precipitation hardening being the classic functions of niobium are rather marginal.
- Unlike other automotive sheet steel, martensitic steel can show brittle fracture behaviour, which is characterized by low energy absorption. This feature is prohibitive for body parts exposed to potential crash impact. Therefore it is important to extend the range of ductile fracture behaviour over the entire temperature range of vehicle operation as well as to increase the ductile fracture toughness.
- This can be achieved by a refinement of the austenite grain structure before quenching into martensite as the martensite sub-structure develops within the prior austenite grains.
- In steels directly quenched from the rolling heat niobium microalloying provides a non-recrystallized (pancaked) microstructure prior to quenching.
- In a reheat-quenching process, as it is used in press-hardening, austenite grain growth is efficiently obstructed by NbC precipitates. These precipitates a formed after hot rolling or by in-situ precipitation during reheating.
- Niobium efficiently reduces the austenite grain size during the hot-rolling stage and prevents austenite grain growth during reheating treatment.
- By enhancing the amount of large-angle grain boundaries, i.e. prior austenite grain boundaries as well as substructure, the resistance against crack propagation is increased. Hence the material becomes tougher. Secondly, the ductile-to-brittle transition temperature is significantly decreased.
Niobium in press-hardening steel
- Press-hardening steel has a fully martensitic microstructure and essentially all effects of niobium apply as outlined above.
- Niobium enhances the robustness of the press-hardening process by obstructing grain coarsening under over-heating conditions, e.g., as consequence of an unexpected stop of the press line.
- Niobium addition in the range of 0.03 to 0.05 was shown to increase the critical bending angle under VDA238-100 test conditions. Many OEMs specify a minimum value for the bending angle.
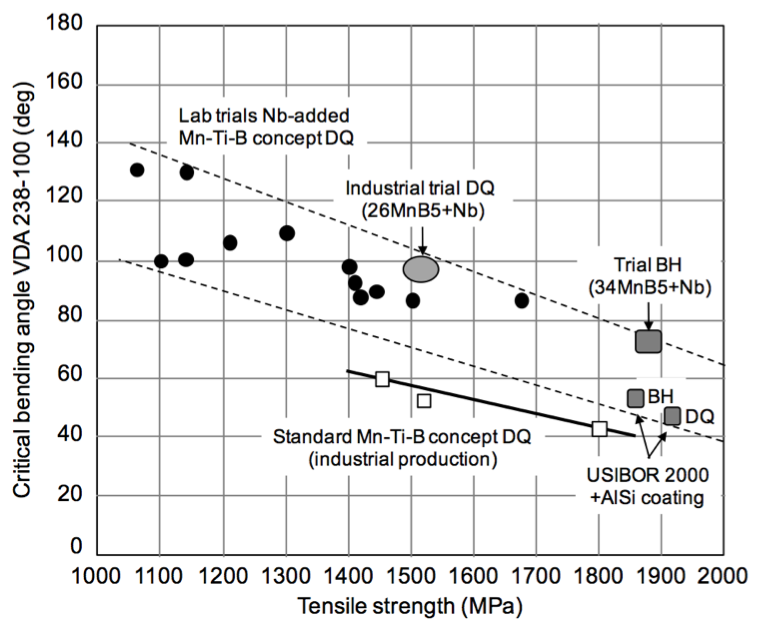
Effect of niobium micro alloying (filled symbols) on the critical bending angle of press-hardening steel in direct quenched (DQ) or bake-hardened (BH) condition
Niobium enhances hydrogen embrittlement resistance
- A severe problem appearing in steels with more than 1000 MPa yield strength is hydrogen embrittlement and the related phenomenon of delayed cracking. This problem inherently applies to all as-quenched martensitic steels.
- Current and on-going research has clearly indicated a beneficial role of niobium by reducing the hydrogen embrittlement sensitivity of martensitic steels. Two principal effects have been identified:
- Enhancement of the total large-angle grain boundary area results in lower specific hydrogen concentration per grain boundary unit area reducing the sensitivity for intergranular fracture.
- Hydrogen trapping by dispersion of ultrafine (<10 nm) sized NbC precipitates. Trapped hydrogen cannot easily diffuse to active damage sites reducing delayed cracking sensitvity.
- Activating both effects together results in considerably increased threshold stress and time to fracture at a given stress level under hydrogen charged conditions.
- Recently developed press hardening steels in the strength range of 1800-2000 MPa integrally implemented these metallurgical mechanisms induced by niobium to comply with OEM demands.